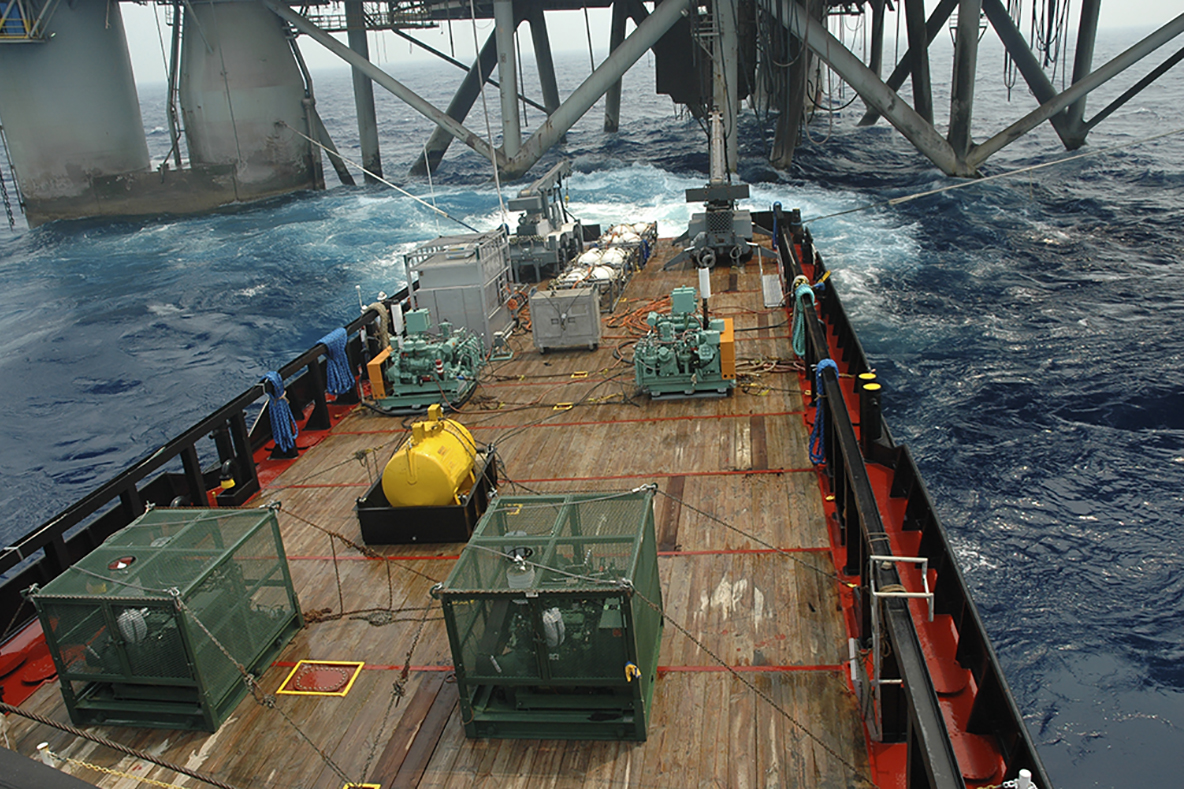
Texas A&M University researchers are studying seal leaks in subsea and aging oil well production facilities with the potential to greatly increase the efficiency of multiple-phase pumping and compressors turbomachinery.
Dr. Luis San Andrés, Mast-Childs Chair Professor in the Turbomachinery Laboratory, along with graduate assistant researcher Xueliang Lu, a Ph.D. candidate in mechanical engineering, conducted a series of measurements on the leakage and dynamic forced performance of wet seals, such as pump liquid seals, mixed with increasing contents of gas. The test results show the gas, or liquid, content affects the system pumping efficiency and reliability, with a dramatic impact on efficiency recorded with only a few droplets of liquid. The experimental results validate mixture model predictions produced by San Andrés in the early 2010s.
By better understanding the role seals have in the machinery, researchers can help industry officials continue to enhance pumping efficiency, increase reliability by reducing vibrations and ensure availability for extended operation times. The researchers said an electric submersible pump (ESP) manufacturer gave them positive comments on their work, and said their data may help them design novel seal types toward improving the life of seals in their ESPs. The current design can only survive 350 hours of operation, about 1/100 of the desired reliability.
The team wrote a paper recording their results, which was recently recognized with the best paper award at the American Society of Mechanical Engineers Turbo-Expo 2017, selected from 133 papers accepted in the Structure & Dynamics Division. Their paper’s title is “Leakage, Drag Power and Rotordynamic Force Coefficients of an Air in Oil (Wet) Annular Seal.”
The Turbomachinery Research Consortium (TRC) has sponsored the research for the past three years.
“TRC members, original equipment manufacturers and end users envision more and more applications of multiple phase pumps for the subsea oil and gas industry,” San Andrés and Lu said. “Wet seals must retain their leakage restriction ability without impairing the dynamic performance of the machinery.”
Follow up lectures are scheduled for presentation at the Asia Turbomachinery Symposium and the Turbomachinery Symposium later this year. More research developments will be published at the Gas Turbine Conference, with another journal paper already accepted.
“The research opens a door for the future research career of Lu as it verifies the likelihood of using air/gas injection to actively control leakage and force coefficient in pump seals and hydraulic turbomachinery in general,” San Andrés said.