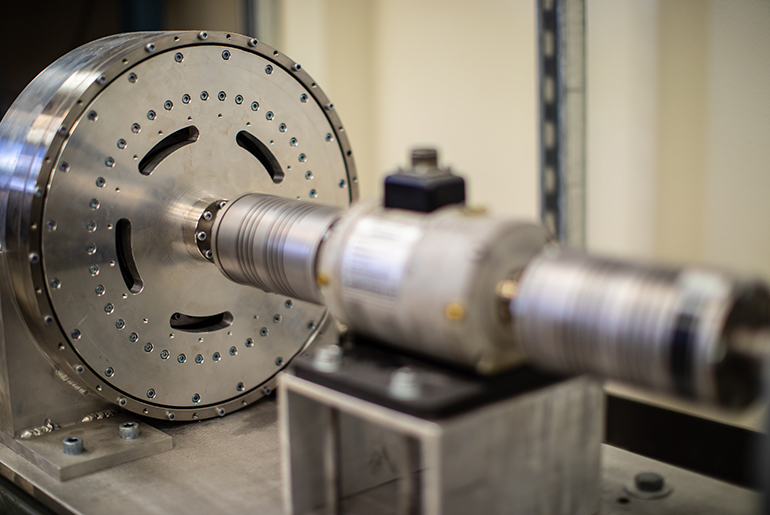
Renewable energy sources, such as wind and wave, can power our world. Currently, mechanical gears are used inside of these energy conversion systems to connect a high-speed electric machine to a low-speed physical energy source. Improving the design of the systems that convert these sources into electrical energy has far-reaching benefits.
Matthew Gardner, a doctoral student in the Department of Electrical and Computer Engineering at Texas A&M University, is studying the use of magnetic gears and their advantages over the traditional mechanically geared machines.
Just like mechanical gears, magnetic gears transform rotational power between different speeds and torques but instead of physically interlocking teeth, they use magnetic fields. By using magnets to transmit torque between the input and output shafts of the gear, they avoid mechanical contact. This provides a number of advantages such as reduced maintenance, reduced acoustic noise and vibrations, and improved overall reliability.
If too much torque is applied to mechanical gears, they may break; if the same happens to magnetic gears, the magnets will simply slip past each other without causing any damage.
In regard to wind and wave energy, some gearing is necessary in machines to avoid the use of an extremely large and expensive generator. For example, special turbines convert the kinetic energy in the wind and water into power. Gearboxes within these mechanically geared systems are subject to severe loads and are often in locations where it is extremely expensive to replace or repair a failed gearbox. With the use of magnetic gears, the cost of maintenance would be significantly reduced.
“Magnetic gears drew my interest because they represent a potentially disruptive innovation in the field of electric machines,” Gardner said. “Much of the research in electric machines represents incremental improvements on the technology that has been developed over the last few hundred years.”
However, magnetic gears are a relatively new area of research and are currently not an industry accepted alternative to mechanical gears. Gardner looks to change that.
He has worked on a project, sponsored by the U.S. Department of Energy, that reduced the cost of wave energy using magnetic gears. Together with the power and automation company ABB, Gardner and his team built a magnetically geared machine prototype that is one of the largest in the world for its particular set of properties. This machine is rated for about 4,000 Newton meters of torque. To put that into perspective, most magnetic gears and magnetically geared machine prototypes in literature are rated for less than 150 Newton meters.
“Our analysis found that using a magnetically geared generator would be about 50 percent smaller, 50 percent lighter and 25 percent less expensive than using a generator without any gearing for this wave energy application,” Gardner said. “On the other hand, reliability concerns ruled out systems involving hydraulics or mechanical gearing.”
Gardner works in the Advanced Electrical Machines and Power Electronics Lab under Dr. Hamid Toliyat, Raytheon Professor. His work has been conducted largely in part with former doctoral student Dr. Matthew Johnson.
"Matthew has done a lot of work that has the possibility to significantly transform the field of electric machines,” Toliyat said.
“I am excited about the opportunity to make a disruptive change in the field of electric machines,” Gardner said. “Magnetic gears and magnetically geared machines offer the possibility to provide a significant, not just incremental, improvement in systems involving electric machines.”