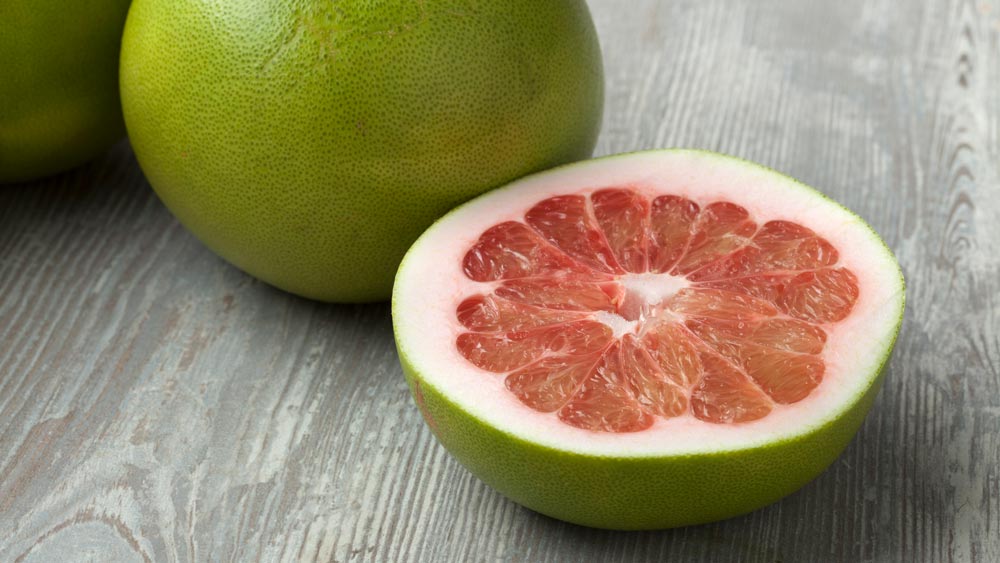
Foam is widely used as a means of protection against impact, shock and vibration. While the current methods for designing foam rely upon uniform pore distribution, nature offers a largely unexplored idea for innovation in impact and collision safety.
Drawing inspiration from the peel of a pomelo fruit, Dr. Daniel McAdams and his team recently became the first to successfully develop a 3D model and simulation of a nonuniform foam material.
This cross between science and nature, and the introduction of irregular porosity into future foam design, has the potential to greatly increase impact resistance.
McAdams serves as the Robert H. Fletcher Professor and associate department head of research and strategic initiatives in the J. Mike Walker '66 Department of Mechanical Engineering at Texas A&M University. His team included doctoral student Guanglu Zhang and former graduate student Jonel Ortiz.
Largest of the citrus fruits, the pomelo originated in South and Southeast Asia. While its size alone is impressive, ranging from the size of a cantaloupe to a small watermelon, McAdams’ team discovered that there is more to this fruit than meets the eye.
“We noticed that a pomelo is able to fall from a height of more than 10 meters without cracking or sustaining inner damage because its peel has outstanding impact damping and energy dissipating capabilities,” said Zhang.
This extraordinary collision resistance stems from the gradient and mix of pore sizes that make up the pomelo peel. Fine and dense near the surface, the pores enlarge and open up the closer they get to the flesh of the fruit; then, nestled against the pulp, they take on an elongated shape and become finer once more.
To utilize this nonuniform porosity, McAdams’ team developed a 3D model of a pomelo peel bioinspired foam using Voronoi tessellation and finite element modeling.
By running virtual case studies with a mathematical-based simulation method, called finite element analysis, the team tested how the proposed foam design might perform in compression and free-fall scenarios.
According to the team, their concept demonstrated both superior impact resistance and impact-dampening potential compared to current foam design.
In addition to providing industry designers a vital development tool, Zhang explained that the team’s modeling will also help lower manufacturing costs.
By setting up a simulation and allowing designers to digitally test various parameter alterations (such as pore size), the researchers’ model helps cut down on the number of physical prototypes that are needed prior to manufacturing. This, along with the reduced weight of their foam, makes the production process more streamlined, cost-effective and efficient.
“Using our model, designers can optimize the foam structure to produce a foam material with better damping and energy dissipating properties,” said Zhang. “So, to achieve the same impact resistance capabilities for an application, like packing, designers can use less of our optimized foam material to attain the same level of protection as the current foam.”
With potential applications ranging from commercial packaging to vehicle collision safety, this research offers engineers and designers a solid foundation on which to build the future of protection.
The researchers’ findings were published in the American Society of Mechanical Engineers Journal of Mechanical Design in a paper titled “A Model for the Design of a Pomelo Peel Bioinspired Foam.”