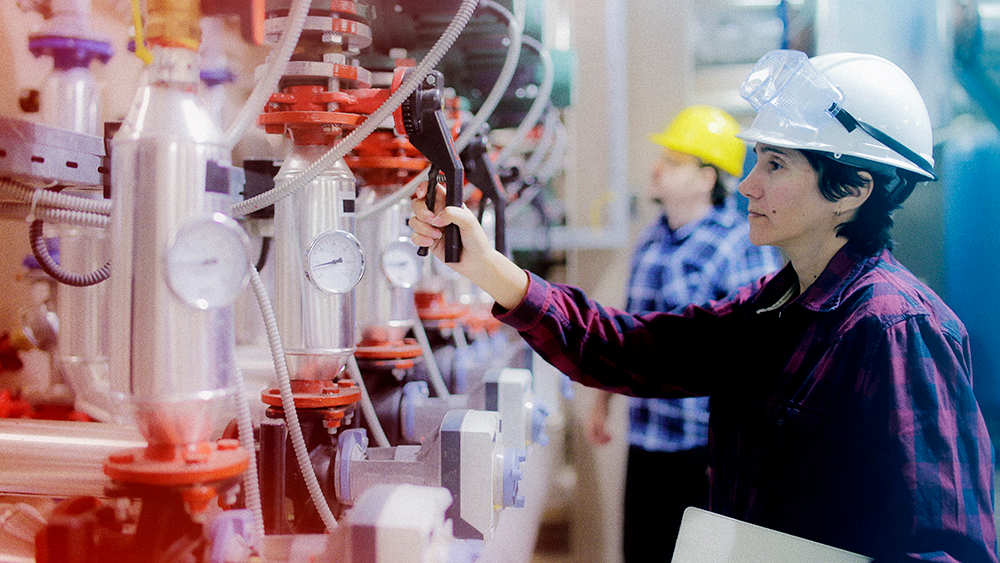
Researchers at Texas A&M University have recently developed a more comprehensive mathematical framework that can help engineers at petrochemical plants to not only reduce production costs and increase economic gain, but also make these factories safer and more environmentally friendly. The researchers said their new algorithm is a one-stop solution that can assist engineers in selecting the most optimal design for chemical processing units within their operating plants.
“The novelty of our algorithm is that it provides a sophisticated decision-making tool that can be used by project engineers to decide between competing designs for their chemical processing units,” said Dr. Prerna Jain, who worked in the Mary Kay O’Connor Process Safety Center as a graduate student at Texas A&M and is currently an engineer at an oil and gas company. “Our tool integrates data from potential equipment hazards, economic data, and more importantly, complex, man-machine interactions to generate a single numerical output. This number then points to a design that maximizes profit while still lowering environmental and hazardous impacts.”
Before petroleum-based products are used for everyday purposes, like heating homes or powering-up vehicles, crude oil passes through a series of processing steps for refinement and packaging. However, each processing phase can be designed in a variety of ways using different technologies and a variable amount of manpower. And so, each design may differ vastly in terms of cost, safety, environmental impact and maintenance.
To select one design among many possible options, engineers often resort to a numerical value called the return on investment. This metric, in its simplest version, indicates the financial benefit or profit resulting from a certain initial monetary investment on a given design. However, engineers often use more extensive algorithms that include factors such as environmental impact and worker safety to compute return on investment values.
But Jain noted that even these more complex algorithms have largely overlooked social factors, such as how often operating procedure manuals at a chemical plant are updated or how frequently equipment maintenance is performed. This human element is important to include while computing the return on investment, she said, because faulty man-equipment interactions often underlie chemical plant disasters, like fires and explosions.
Dr. Mahmoud El-Halwagi, professor and the Bryan Research and Engineering Chair in the Artie McFerrin Department of Chemical Engineering at Texas A&M, pointed out that social and safety factors are typically considered after major design decisions regarding the chemical plant have been made. “At this stage, key design components are already finalized, and it becomes rather difficult to make substantial design modifications,” he said.
To address these deficits, Jain and her team developed an even more elaborate mathematical framework that could be implemented when designing chemical processing units. Furthermore, their algorithm now included man-machine interactions.
In the new algorithm, they plugged in a quantity called resilience, or the ability of a chemical plant to recover from a stressed state.
“Just as a rubber band can only be stretched to its elastic limit before it breaks, chemical plants, if used to their maximum capacity and without safety measures in place, can degrade, leading to catastrophes,” said Jain. “By incorporating resilience into our algorithm, we wanted to include the complex interactions between man and technology that can affect resilience and, by extension, the estimation of the return of investment.”
Once the algorithm was fully developed, the researchers used it to compare different designs of gas compressor systems frequently used in chemical plants. In particular, they contrasted the value of the return on investment for a compression system existing in a chemical plant with five other hypothetical designs.
Jain and her colleagues found that after taking social factors into account, the most promising compressor system design was not the one that was already in the existing plant, but the one that the researchers had created.
Jain noted that their observations indicate the feasibility of using their algorithm to evaluate new process design ideas that exist in theory but haven’t been put to the test in an existing plant.
“There is often a hesitation in the energy industry to invest in a new process design if it hasn’t been evaluated yet,” said Jain. “With our algorithm, we now have the ability to brainstorm ideas for new process designs and test them virtually, without really needing them to be physically set up and running. Moreover, we can feed the algorithm with numbers corresponding to different social factors pertaining to chemical plants. In the process, we might stumble upon a new, better design that is safer for workers and kinder to the environment.”
Other contributors to the research included Kariana Mareno-Sader Tenorio from the Department of Chemical Engineering, University of Cartagena, Colombia; Luis Carlos Ballestas from Ecopetrol SA, Columbia; and Dr. M. Sam Mannan from the chemical engineering department and executive director of the Mary Kay O'Connor Process Safety Center at Texas A&M.
This work was supported by funds from the Mary Kay O’Connor Process Safety Center.