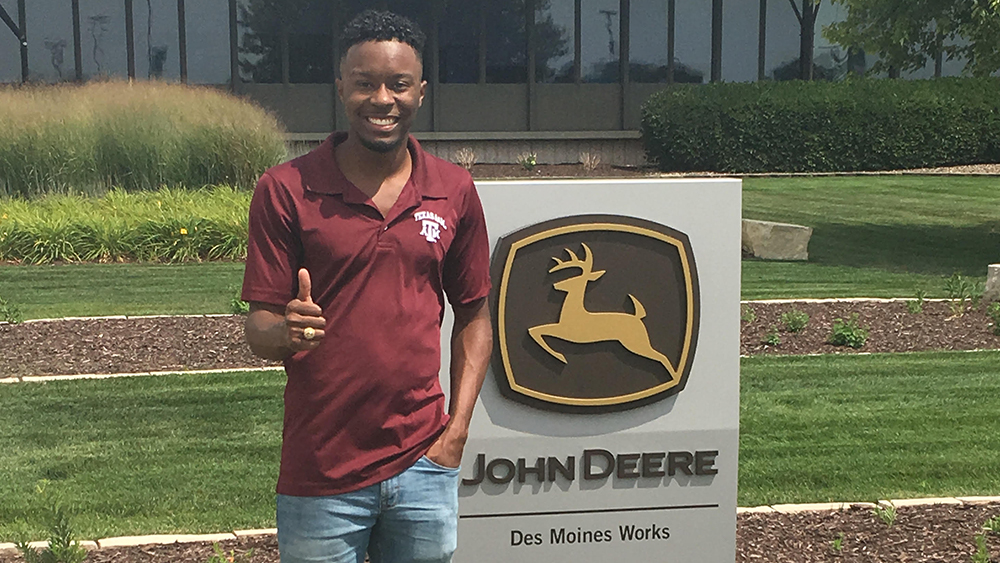
John Deere is well known for tractors, machinery and a particular shade of green, which can be seen mowing lawns and plowing fields across the world. Behind the scenes, John Deere also cultivates the minds of many students through internships, including those for industrial engineering students.
Zach Reece, who graduated in May, interned with John Deere last summer and learned how manufacturing and engineering connect. Reece had a previous internship in construction project management, but had not worked in manufacturing before. Since his internship with John Deere, he has accepted a role in manufacturing as an industrial engineer associate at Lockheed Martin, where he will put his his industrial engineering education to work.
While he was not always an industrial engineering student, Reece is glad he transferred to industrial engineering.
“I came across ISEN by accident. After I learned more about business and entrepreneurship, I made the switch to the department and loved it ever since,” Reece said. “Joining ISEN is the best decision I made in my collegiate career. I loved both my classes and my professors, and I couldn't imagine what my life would be like if I wasn't in ISEN.”
We spoke with Reece about his experience as an intern with John Deere and how his industrial engineering education has prepared him for the future.
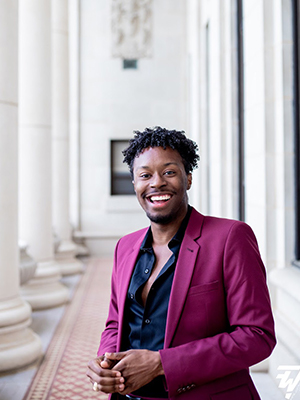
Q: What was it like working for John Deere?
A: John Deere provided me with the internship of a lifetime. I lived in Waterloo, Iowa, with 120 other interns and met some truly exceptional people. Two of my roommates worked in the same facility with me, and we all got great exposure to heavy equipment assembly like tractors and other machinery. Now I won’t say I can build a tractor by myself after my time at John Deere, but I am confident enough to try to if I have some help.
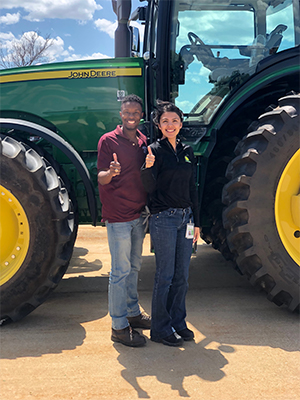
Q: What were you doing on the job during your internship?
A: I worked in the operations department, which includes the first-line supervisors of the assemblers for the 8R tractors. Assemblers are the individuals that put the tractors together. My first week there was spent walking the production line and building a mind map of the assembly process. You aren’t expected as an intern to come for three months and command a group of workers, so instead, I provided support by automating data analysis. I struggled with Excel macros for weeks, but everything finally clicked within my last days of the internship. My favorite parts of the job were getting to know the operators — there were 50-75 operators within my department — and being able to see the different aspects of manufacturing.
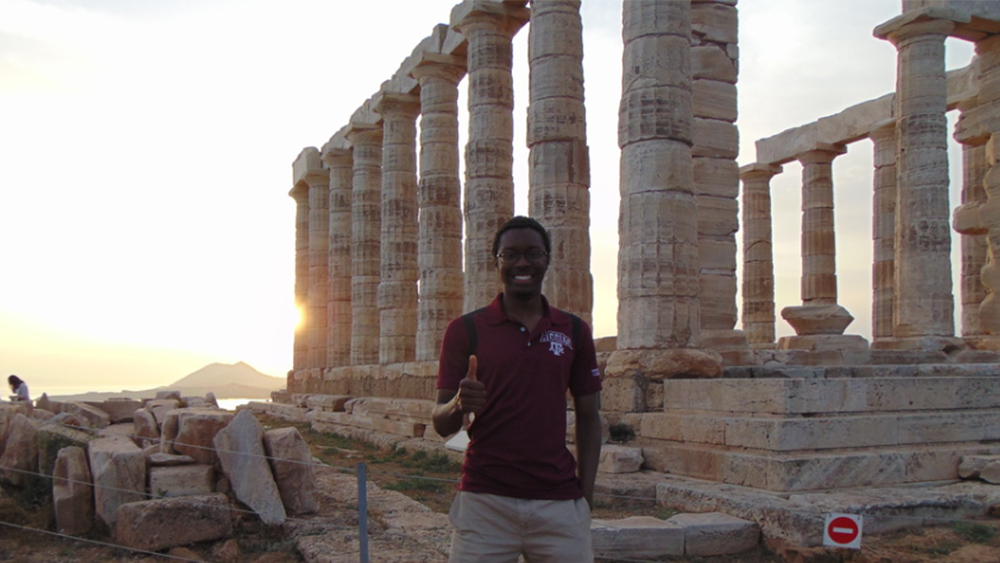
Q: What did you learn from your internship?
A: Since I worked so closely with the production line, I learned the relationship between the operators and the supervisors in a union factory. Last summer, John Deere experienced a lot of disruption due to changes in trade regulations and product development. It was amazing to learn how to react in a constantly changing environment and it prepared me for whatever happens in my next role.
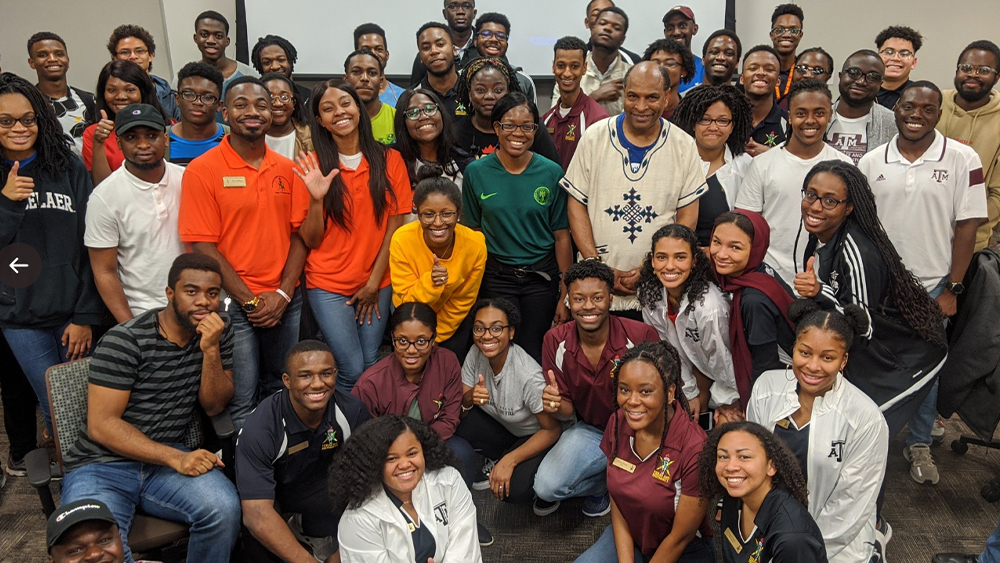
Q: You recently graduated. Congrats! What will you be doing as new graduate?
A: I really enjoy manufacturing. Dr. Elwany and researchers in his lab have helped me deepen my passion for additive manufacturing and 3D printing. I have accepted a position with Lockheed Martin that exposes me to a holistic manufacturing experience, and I can foresee specializing designs for additive manufacturing.
Most importantly, I have thoroughly enjoyed my time in industrial engineering. The greatest decision I have made in my collegiate career was switching into industrial engineering. None of this would have been possible if I hadn’t made that choice. While it’s unfortunate that commencement is postponed, I appreciate the time I have to thank those that have helped me make it this far, including many of my professors.