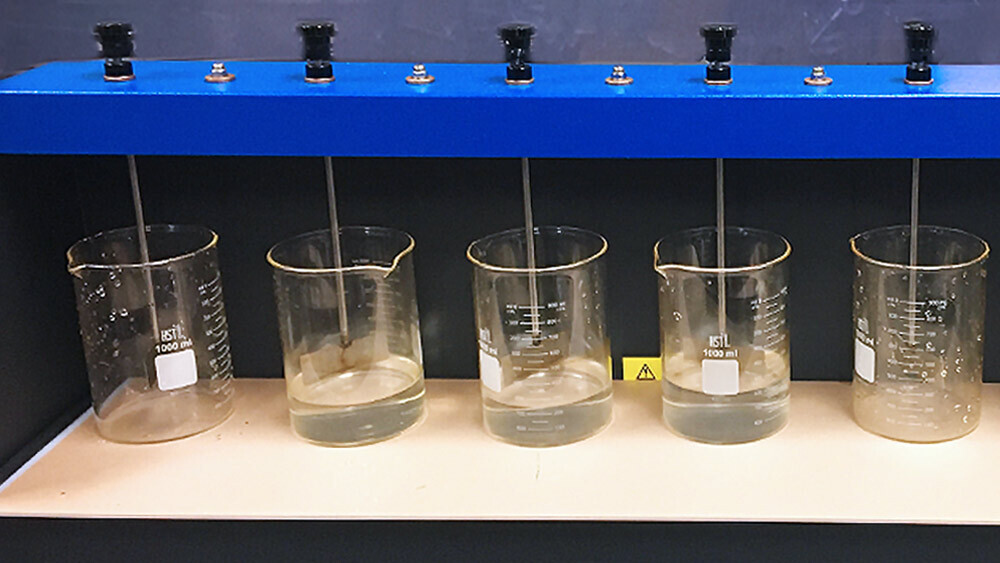
Hydraulic fracturing, an oil-recovery process in shale reservoirs, uses tremendous amounts of fresh water to crack the shale rock and free trapped oil and gas. Some of this water eventually flows back to the surface, where it can be reclaimed and treated for reuse. However, this flowback water flushes out another kind of fluid from the reservoir, called produced water. Since produced water is severely contaminated and considered a waste product, it is commonly injected underground, where it poses a threat to clean water supplies and ground stability.
Dr. Berna Hascakir, associate professor in the Harold Vance Department of Petroleum Engineering at Texas A&M University, is investigating simple and cost-effective methods that can significantly clean produced water so it can be further treated and used in hydraulic fracturing processes, saving millions of gallons of fresh water for better use elsewhere.
Her research is part of a water management project headed by the Berg-Hughes Center for Petroleum and Sedimentary Systems and funded by University Lands with a $771,500 grant. University Lands manages the surface and mineral interests of over 2 million acres in West Texas, and its governing board is highly involved in environmental stewardship, so they are keen to find a way to reuse produced water rather than write it off as waste. If the water can be cleaned enough for use in hydraulic fracturing, this saves fresh water supplies and benefits both the environment and the public.
Injecting pressurized fresh water underground is necessary for oil recovery in shale. While much of this water remains in the underground reservoir, what flows back up to the surface contains dissolved salts, minerals and other solids that must be removed before reuse. However, the fluid flushed out the reservoir, known in the industry as produced water, has a far greater level of total dissolved solids (TDS) because it has been in the reservoir for centuries. For instance, the salt levels in produced water can be 10 times higher than seawater, about 70 teaspoons per quart or 350 grams per liter. Factor in the other contaminant levels in produced water, and the volume of TDS is incredibly tough to remove.
Since produced water is unfit to recycle for human consumption, it has been considered for reuse in hydraulic fracturing activities to save available fresh water sources for other needs. However, Hascakir noted that this use of produced water is hardly advantageous unless its TDS levels are significantly reduced.
“Opening fractures underground by injecting produced water into the tiny shale fractures means the fractures can get blocked immediately by any solids suspended or dissolved in the water,” said Hascakir. “This becomes an obstacle for oil production pathways.”
The salts in produced water are dissolved as free ions. Currently, these ions can only be removed using advanced water treatment methods, such as reverse osmosis, ultrafiltration and nanofiltration. However, the salt levels of produced water are too high for these methods to handle, so Hascakir must reduce the salinity before they can be used. This catch-22 situation makes removing the salts difficult but not impossible.
Many of the other solids in produced water naturally attract salt and are suspended in the form of colloids, which are larger in size than the salt ions. Hascakir and her student researcher, Damir Kaishentayev, are exploring three basic water treatment methods, alone and in combinations, to remove these larger solids while also reducing salt levels enough for the advanced treatment methods to work.
For the first method, coagulation, Hascakir is taking advantage of some colloids’ ability to chemically or electrically attract together. For example, blood platelets, a type of colloid, can form clots. Hascakir said that many of the suspended solids have negative electrical charges. She is using chemicals to reverse these negative repulses so these colloids cling to each other and pull salt ions in with them when they form heavy clots of molecules.
For non-charged colloids, Hascakir is using flocculation, a chemical process that pulls the colloids into clumps, called flocs, with the use of polymers. She is testing various polymers to see which ones allow the captured solids to take salts with them into the flocs.
The third method is sedimentation. Coagulation and flocculation need rapid stirring or agitation for chemical reactions to occur. The stillness of sedimentation encourages larger solids, coagulations and flocs to either gradually float to the surface or sink to the bottom of the treatment tanks.
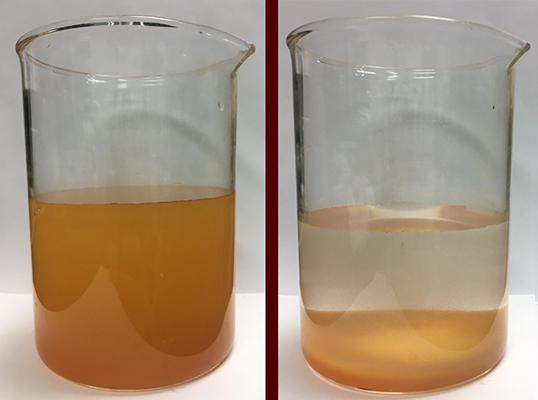
Hascakir’s work is the initial cycle of the Berg-Hughes study. Each of her treated water samples goes on for further testing. A chemical researcher will determine how well the samples respond to reverse-osmosis and other treatments. Agricultural researchers will test plant reactions to the treated water. Economic researchers will calculate water treatment costs based on Hascakir’s methods to see if it is cost-effective for companies to fund. Finally, geologists will analyze how the treated water could affect groundwater should the two intermingle.
The project aims to find methods that can treat tremendous quantities of produced water cheaply and effectively so it can be used instead of stored away as waste that might contaminate the environment. That goal is crucial, said Hascakir. The majority of new wells drilled in the U.S. are hydraulically fractured. With an average of 3-7 million gallons of water used for every hydraulic fracturing treatment, the amount of produced water flushed out of reservoirs is increasing rapidly.
“Produced water is a huge problem,” said Hascakir. “If we find a solution, a reuse for the University Lands’ produced water, it can be applied to every other area using hydraulic fracturing. This is really exciting for me because the project connects my environmental engineering background with my petroleum engineering work and is producing a unique solution for hydraulic fracturing water needs.”