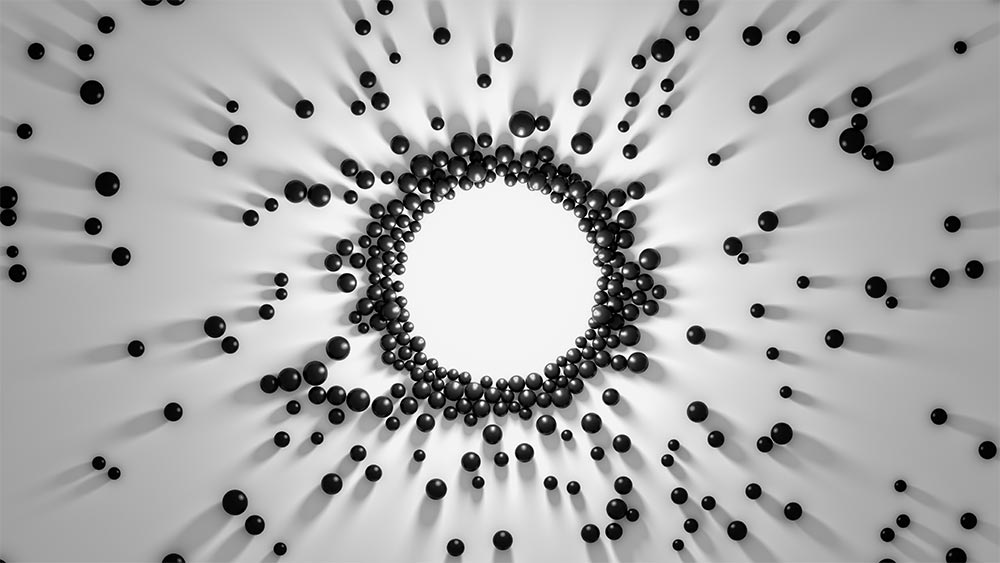
When one of the largest modern earthquakes struck Japan on March 11, 2011, the nuclear reactors at Fukushima-Daiichi automatically shut down, as designed. The emergency systems, which would have helped maintain the necessary cooling of the core, were destroyed by the subsequent tsunami. Because the reactor could no longer cool itself, the core overheated, resulting in a severe nuclear meltdown, the likes of which haven’t been seen since the Chernobyl disaster in 1986.
Since then, reactors have improved exponentially in terms of safety, sustainability and efficiency. Unlike the light-water reactors at Fukushima, which had liquid coolant and uranium fuel, the current generation of reactors has a variety of coolant options, including molten-salt mixtures, supercritical water and even gases like helium.
Dr. Jean Ragusa and Dr. Mauricio Eduardo Tano Retamales from the Department of Nuclear Engineering at Texas A&M University have been studying a new fourth-generation reactor, pebble bed reactors. Pebble-bed reactors use spherical fuel elements (known as pebbles) and a fluid coolant (usually a gas).
“There are about 40,000 fuel pebbles in such a reactor,” said Ragusa. “Think of the reactor as a really big bucket with 40,000 tennis balls inside.”
During an accident, as the gas in the reactor core begins to heat up, the cold air from below begins to rise, a process known as natural convection cooling. Additionally, the fuel pebbles are made from pyrolytic carbon and tristructural-isotropic particles, making them resistant to temperatures as high as 3,000 degrees Fahrenheit. As a very-high-temperature reactor (VHTR), pebble-bed reactors can be cooled down by passive natural circulation, making it theoretically impossible for an accident like Fukushima to occur.
However, during normal operation, a high-speed flow cools the pebbles. This flow creates movement around and between the fuel pebbles, similar to the way a gust of wind changes the trajectory of a tennis ball. How do you account for the friction between the pebbles and the influence of that friction in the cooling process?
This is the question that Ragusa and Tano aimed to answer in their most recent publication in the journal Nuclear Technology titled “Coupled Computational Fluid Dynamics–Discrete Element Method Study of Bypass Flows in a Pebble-Bed Reactor.”
“We solved for the location of these ‘tennis balls’ using the Discrete Element Method, where we account for the flow-induced motion and friction between all the tennis balls,” said Tano. “The coupled model is then tested against thermal measurements in the SANA experiment.”
The SANA experiment was conducted in the early 1990s and measured how the mechanisms in a reactor interchange when transmitting heat from the center of the cylinder to the outer part. This experiment allowed Tano and Ragusa to have a standard to which they could validate their models.
As a result, their teams developed a coupled Computational Fluid Dynamics-Discrete Element Methods model for studying the flow over a pebble bed. This model can now be applied to all high-temperature pebble-bed reactors and is the first computational model of its kind to do so. It’s very-high-accuracy tools such as this that allow vendors to develop better reactors.
“The computational models we create help us more accurately assess different physical phenomena in the reactor,” said Tano. “As a result, reactors can operate at a higher margin, theoretically producing more power while increasing the safety of the reactor. We do the same thing with our models for molten-salt reactors for the Department of Energy.”
As artificial intelligence continues to advance, its applications to computational modeling and simulation grow. “We’re in a very exciting time for the field,” said Ragusa. “And we encourage any prospective students who are interested in computational modeling to reach out, because this field will hopefully be around for a long time.”