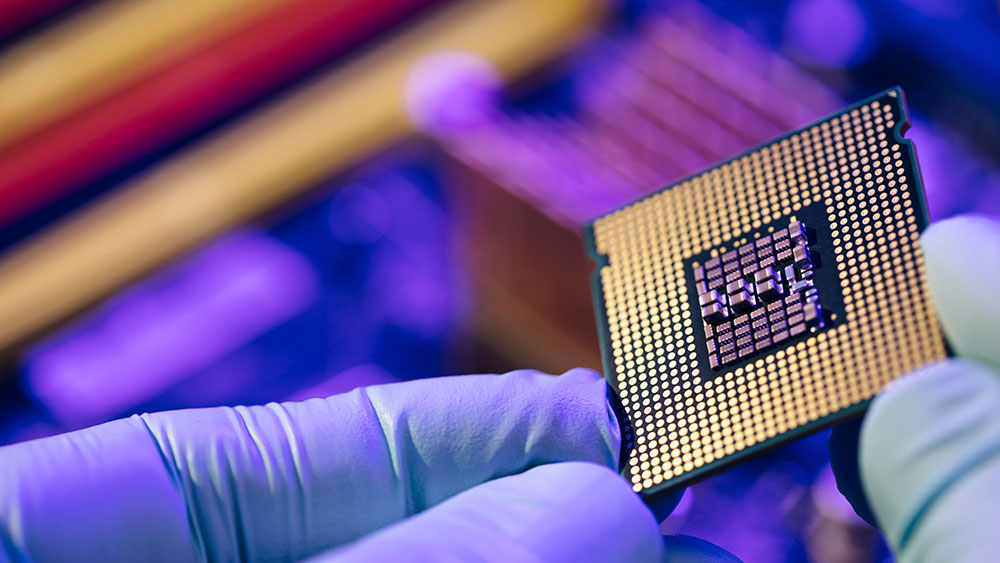
Chances are you’ve either heard of the global semiconductor chip shortage or been personally affected by it when looking into purchasing a new or used vehicle over the last year and a half. You might be wondering why this has happened and how the situation can be remediated. Two faculty members in the Department of Electrical and Computer Engineering at Texas A&M University — Dr. Paul Gratz, professor, and Stavros Kalafatis, professor of practice and associate department head — are weighing in to provide answers.
Over the last 20 years, the semiconductor chip manufacturing process underwent a large shift, resulting in most fabrication occurring overseas. This change worked well for the semiconductor industry pre-pandemic because manufacturers were able to design the chips in house and have them fabricated for much less at overseas locations.
In 2020, when the pandemic shocked the world, consumers were purchasing less of everything and, subsequently, tech companies stopped purchasing inventory. When the world kept spinning in a new virtual way, with many working from home, items such as laptops and other electronics became in extremely high demand. Personal computer sales grew by 11% in 2020 — the highest growth for that technology in a decade.
This unexpected demand shocked many in the electronics business. No one was prepared for all that ensued in 2020, but the automotive industry was particularly affected by the shortage and continues to feel those consequences today. This, in part, stems from the decision to cease orders for microcontrollers and other chips early in the pandemic due to the prediction that consumers would not need or want to buy a car during that time. Coupled with these chips being used for cars as well as other technology — such as smartphones and laptops — the stock is simply not available at this time.
"There are only so many chips that can be built per unit of time," Gratz explained. "Right now, all of the fabrication facilities are running out of inventory and are still not able to keep up with the demand. It takes a long time (around two years) to build new ones, so we are stuck with what we have until more fabrication facilities can come online."
Kalafatis, a former senior director with Intel, explained that Intel is the last volume processor manufacturer in the United States with fabrication facilities that are local and what that means for the computer and automotive industry, which both use these chips.
“A lot of these high-end fabs that are local are targeted toward the production of microprocessors,” Kalafatis said. “So that helps the laptop and desktop market, but it doesn't help automotive very much.”
The International Data Corporation predicts the semiconductor market to reach $600 billion by 2025 — representing a compound annual growth rate of 5.3% through the forecast period, which is higher than the typical 3-4% mature growth seen historically.
So, where do we go from here?
Gratz says a start would be to house more fabrication facilities in the U.S. In addition to benefiting national security, this could help with fabrication time in the long run. In the short term, chip companies such as Taiwan Semiconductor Manufacturing Company, Intel and Samsung are actively spending hundreds of billions on increasing capacity to meet the demand. Despite these efforts, both Gratz and Kalafatis believe it will take at least six months to a year for the semiconductor chip industry to get back to more normal operating procedures.
Closer to home, the Texas A&M Engineering Experiment Station’s Hewlett Packard Enterprise Center for Computer Architecture Research, made possible with a generous donation from Hewlett Packard Enterprise, is providing the capability for researchers to design novel semiconductor chips that will change the landscape of computer architectures. Through academic-industry collaboration, the center is working to ultimately make a long-term impact in this area of semiconductor chips.