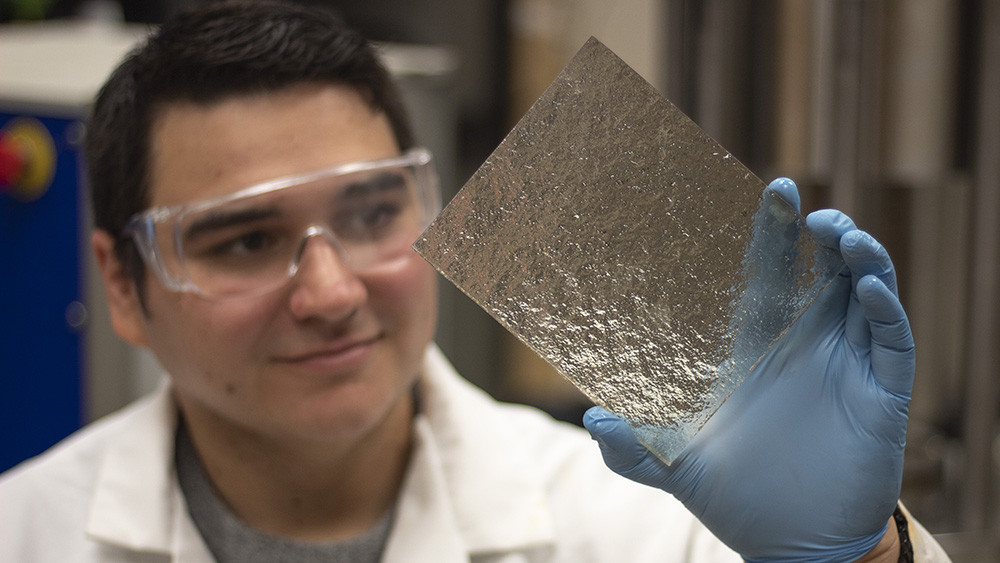
The oil and gas industry has modified the proppants and diverters they use in fracture processes to improve oil recovery in shale reservoirs over the years. But the efforts are based on guesswork since proppant and diverter behavior is impossible to observe as it occurs entirely out of sight downhole.
Texas A&M University graduate researcher Gabriel Tatman has utilized 3D printing to recreate fractures in a way that reveals proppant and diverter behavior as part of a joint industry project. His novel use of clear models created from actual rock fracture data uncovered these unseen behaviors and led to the unique ability to repeat fracture flow experiments in exacting detail.
The project is a collaboration between Texas A&M and the Colorado School of Mines, where actual proppant transport experiments occur. The goal is to identify conditions that lead to maximized proppant placement and what proppant concentrations and types perform the best in various rock geometries. This will improve hydraulic fracturing efforts in oil recovery.
"We're not the first to 3D print rock surfaces, but we are the first to do resin 3D printing for this particular application," said Tatman.
Oil recovery in shale reservoirs usually begins with hydraulic fracturing, where fluid is forced into the rock formation at high pressures to fracture or crack the shale. Proppants, different sized grains of sand, are flushed down in a fluid slurry to hold these fractures open after the high pressure is released so oil and gas can flow to the well. Diverters, which are chemical or mechanical materials that can later be dissolved or recovered, are sometimes injected to strategically block main slurry paths so proppants are forced into new channels to create complex fracture geometries. The process usually goes unseen, but 3D printing technology is helping to change that.
When he was an undergraduate student in the Harold Vance Department of Petroleum Engineering, Tatman shared his hobby interest in 3D printing with Dr. Ding Zhu, professor and McCain Engineering Chair. He even 3D printed a rock casting containing a complex, acid-dissolved flow channel structure while he was a student in her class. Impressed, Zhu encouraged Tatman to experiment with potential applications in research.
Being able to bring the hobby side of my life to the research side and integrate both into something productive has been something I'm really proud of.
After receiving his bachelor's degree, Tatman joined Zhu and Regents Professor and Noble Chair Dr. Dan Hill to begin his graduate studies. His work with their team researching hydraulic fracturing produced clear 3D-printed samples with micrometer-level details of fracture surfaces. When flushed through these transparent fracture models, the proppant and diverter behavior could be directly observed.
Seeing actual proppant behavior is groundbreaking, but the project also applies 3D printing to fracture conductivity in an unprecedented way.
In the past, researchers built laboratory-scale equipment to study how effectively proppants allow oil and gas to flow in fractures, a process called conductivity. Still, the equipment was usually constructed with smooth walls where natural rock fracture surfaces are very irregular.
Rough artificial fracture surfaces can be easily created in detail with 3D printing thanks to current equipment. The drawback is 3D printing resins are not strong enough for experiments requiring actual rock-like strength. So Tatman's 3D printouts are used as molds to create artificial rock structures out of high-strength cement that can capture complex surface geometries. And these artificial samples can be infinitely cast from the molds, leading to consistent and repeatable test bases for more accurate research results.
"We can simulate fracture surfaces by using common geostatistical approaches that capture the characteristics of a particular formation," Tatman said. "With 3D printing, we can create physical versions of these simulated surfaces for experiment applications."
Since fracture surface characteristics can vary for each shale formation, Tatman said the team will eventually construct a database of proppant transport behavior in different reservoirs.
He won't see the end of the project because he leaves after graduation in the spring for a full-time position in the industry, but Tatman is excited to be part of the cutting-edge research laying the foundation for future work. He also looks forward to seeing 3D printing take on other investigations, such as plugging agent behaviors in wormhole geometries formed within acid-treated reservoirs.
"(In) the past five years, the level of development seen in the 3D printing world has been phenomenal," Tatman said. "3D printing has been something I have been passionate about since high school. Being able to bring the hobby side of my life to the research side and integrate both into something productive has been something I'm really proud of."