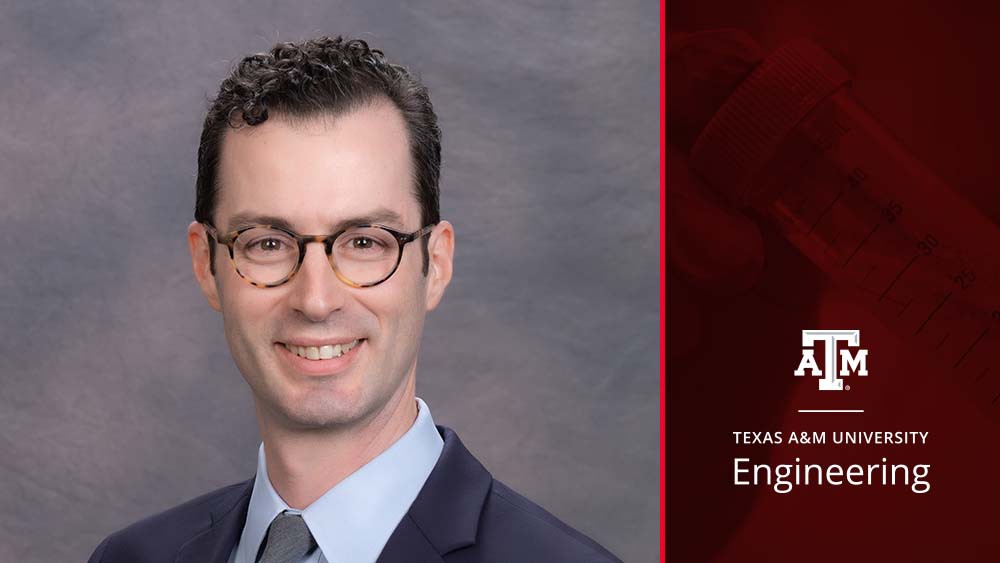
Dr. Stephen Raiman is researching additively manufactured, ultra- high-temperature ceramics as construction materials for solar power systems. |
Image: Texas A&M College of Engineering
A team of researchers, including Dr. Stephen Raiman from the Department of Nuclear Engineering, has received a grant from the U.S. Department of Energy Solar Energy Technologies Office to investigate additively manufactured, ultra-high-temperature ceramics as construction materials for heat exchangers in concentrating solar power (CSP) systems.
Through this research, the team seeks to improve the economic viability of concentrating solar power by reducing maintenance costs, improving thermal efficiency and lowering construction costs.
Dr. James Kelly from Lawrence Livermore National Laboratory (LLNL) is the lead principal investigator, while Raiman and Bruce Pint at Oak Ridge National Laboratory (ORNL) are co-principal investigators. The grant totals $1.6 million, with $300,000 going to Texas A&M University.
In CSP, the sun’s rays are used to heat a high-temperature chloride salt mixture to temperatures up to 800 degrees Celsius. The salt mixture flows through a heat exchanger to capture the energy and transfer it to flowing supercritical carbon dioxide (sCO2). It is challenging to find materials for high-temperature heat exchangers that can resist the corrosive molten salt and sCO2 simultaneously.
LLNL produces ceramics capable of withstanding high-temperature corrosive environments using a unique additive manufacturing process. At Texas A&M, Raiman, assistant professor, will be testing the materials in molten chloride salts to discover how to optimize their ability to resist corrosion and degradation in service.
“Additive manufacturing frees designers to use complex geometries that are not possible with conventional manufacturing,” said Raiman. “This enables higher performance heat exchangers that can fit into smaller spaces.”
His team will also be developing a robust metal-to-ceramic joining process that will enable ceramic heat exchangers to be attached to metal pipes. ORNL will be testing the materials in sCO2 to determine how they withstand corrosion and mechanical stresses in service-relevant environments.
“Due to the combination of corrosive process fluids and high temperatures, heat exchangers are among the most demanding components from a materials perspective,” said Raiman. “To improve thermal efficiency, it is desirable to make the walls as thin as possible, which makes them more susceptible to failure. The use of advanced materials opens up new design possibilities that can improve performance, reduce costs and extend service lifetimes.”
The U.S. Department of Energy Solar Energy Technologies Office supports early-stage research and development to improve the affordability, reliability, and performance of solar technologies on the grid.
Through this research, the team seeks to improve the economic viability of concentrating solar power by reducing maintenance costs, improving thermal efficiency and lowering construction costs.
Dr. James Kelly from Lawrence Livermore National Laboratory (LLNL) is the lead principal investigator, while Raiman and Bruce Pint at Oak Ridge National Laboratory (ORNL) are co-principal investigators. The grant totals $1.6 million, with $300,000 going to Texas A&M University.
In CSP, the sun’s rays are used to heat a high-temperature chloride salt mixture to temperatures up to 800 degrees Celsius. The salt mixture flows through a heat exchanger to capture the energy and transfer it to flowing supercritical carbon dioxide (sCO2). It is challenging to find materials for high-temperature heat exchangers that can resist the corrosive molten salt and sCO2 simultaneously.
LLNL produces ceramics capable of withstanding high-temperature corrosive environments using a unique additive manufacturing process. At Texas A&M, Raiman, assistant professor, will be testing the materials in molten chloride salts to discover how to optimize their ability to resist corrosion and degradation in service.
“Additive manufacturing frees designers to use complex geometries that are not possible with conventional manufacturing,” said Raiman. “This enables higher performance heat exchangers that can fit into smaller spaces.”
His team will also be developing a robust metal-to-ceramic joining process that will enable ceramic heat exchangers to be attached to metal pipes. ORNL will be testing the materials in sCO2 to determine how they withstand corrosion and mechanical stresses in service-relevant environments.
“Due to the combination of corrosive process fluids and high temperatures, heat exchangers are among the most demanding components from a materials perspective,” said Raiman. “To improve thermal efficiency, it is desirable to make the walls as thin as possible, which makes them more susceptible to failure. The use of advanced materials opens up new design possibilities that can improve performance, reduce costs and extend service lifetimes.”
The U.S. Department of Energy Solar Energy Technologies Office supports early-stage research and development to improve the affordability, reliability, and performance of solar technologies on the grid.