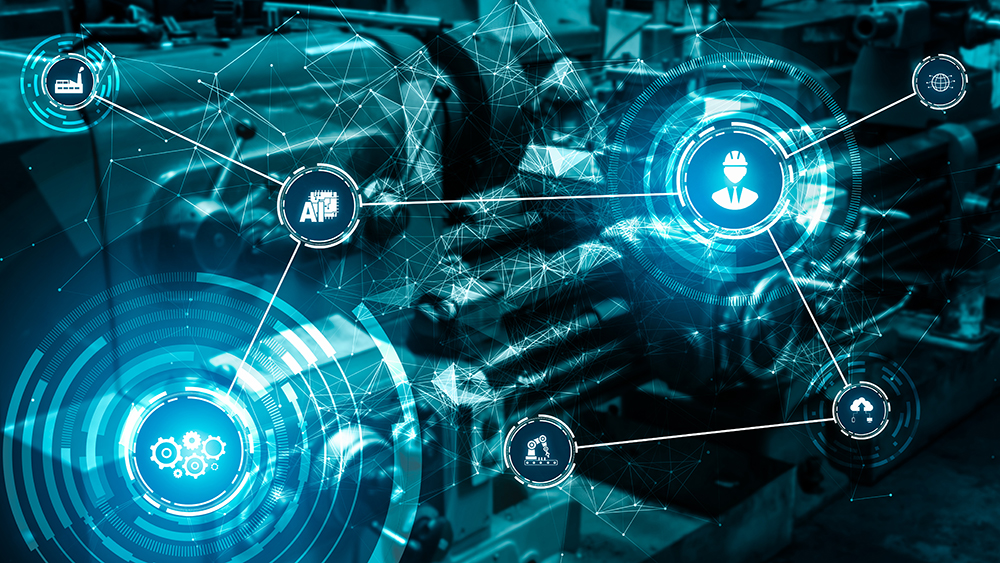
Smart manufacturing — or the use of emerging, advanced technologies to increase the efficiency of traditional manufacturing processes — is creating a more agile and productive industrial base. Experts with the SecureAmerica Institute (SAI) and Texas A&M University College of Engineering explain why leveraging these innovations is crucial to advance the industry forward.
“Smart manufacturing is a national priority as detailed in the White House Critical and Emerging Technologies Report,” said Rob Gorham, SAI executive director. “The SecureAmerica Institute continues to integrate these capabilities into manufacturing ecosystems across Texas and the nation.”
The term smart manufacturing arose in the mid-2000s, prompted by the arrival of new technologies such as 3D printing (additive manufacturing) and artificial intelligence. Other concepts like “digital manufacturing” and “cyber manufacturing” converge under the smart manufacturing label. At this time, global standards are still being developed to further define smart manufacturing approaches.
“Smart manufacturing processes provide better connection and communication across manufacturing systems,” said Dr. Alaa Elwany, associate professor in the Wm Michael Barnes ’64 Department of Industrial and Systems Engineering at the Texas A&M University College of Engineering. “They help to streamline procedures, so systems are not operating as silos.”
“Asset management and quality assurance are two areas smart manufacturing processes can vitally enhance the manufacturing industry,” said Dr. Satish Bukkapatnam, professor of industrial and systems engineering and director of the Texas A&M Engineering Experiment Station Institute for Manufacturing Systems. “Remote servicing of machines ensures plants can focus on producing parts instead of repairing them, while the introduction of sensor technology assures product quality and production efficiency.”
Imagine standing inside a single, large manufacturing plant with multiple machines and operators. Each system should be communicating to share resources, trigger maintenance activities, order spare parts, and more — all at one location. This type of connectivity is also needed between multiple plants, at different locations across the United States, within an enterprise that demands all machines communicate effectively with one another.
“Smart manufacturing technologies aid in identifying problem areas, so the overall network of connected manufacturing devices produces competent and profitable operations,” Elwany said.
Digital twins are a powerful smart manufacturing tool that support production. A digital twin is the creation of an identical virtual product or system before a physical prototype is manufactured. This virtual environment allows manufacturers to run simulations, iterations and testing on the design of a product to ensure viability before extensive production costs are incurred.
The widespread industry adoption of smart manufacturing still faces barriers, especially for small-to-medium manufacturing enterprises (SMEs), due to cost and lack of workforce training.
“If small and medium companies don’t adapt, they will be at a great disadvantage,” Bukkapatnam said. “There will be a digital divide between businesses who have advanced capabilities and others who don’t. Smart manufacturing helps the industry create a level playing field where large companies can thrive and SMEs who are given digital resources are not left behind.”
“Organizations like the SecureAmerica Institute are integral to provide technical expertise needed for the wider digital transformation of manufacturing,” Elwany said. “SAI thought leadership is our strongest resource to develop more certificate programs, continuing education programs and courses to train the future manufacturing workforce in emerging technologies.”