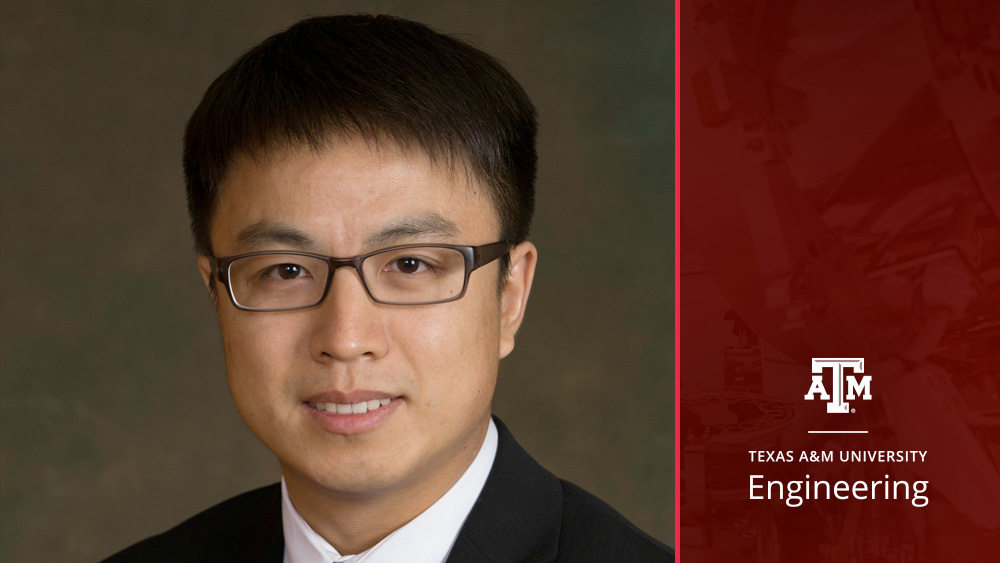
Ceramic additive manufacturing has vast potential to transform numerous industries, from health care to aerospace to national security, and increase the economic competitiveness of the United States.
Dr. Chao Ma, assistant professor in the Department of Engineering Technology and Industrial Distribution at Texas A&M University, will generate new insights necessary for binder jetting to produce dense ceramic parts.
Ma recently received the Faculty Early Career Development (CAREER) Award from the National Science Foundation (NSF) — one of the most prestigious awards for up-and-coming researchers. The grant provides funding to support promising integrated research and education projects.
Ma will use the CAREER award to create a new granulated powder and an innovative powder bed formation method that will work synergistically to strengthen the use of advanced ceramics.
Advanced ceramic materials provide a combination of excellent properties, including high stiffness, high hardness, and superior chemical, wear and heat resistance. Because of these properties, advanced ceramics play a vital role in diverse industries and applications such as joint prostheses, aircraft engines, ballistic armor, chemical-resistant impellers, and heat exchangers. These products are created by traditional ceramic manufacturing with severe geometric constraints.
But Ma says ceramic additive manufacturing can release these constraints and bring revolutionary impacts to the industry. The implications are far-reaching, with potentially positive effects on the environment, for example. Without this geometric limitation, producing dense ceramic parts could include chemical-resistant pumps and high-temperature heat exchangers to help chemical manufacturers and energy industries purify materials and generate clean energy more efficiently.
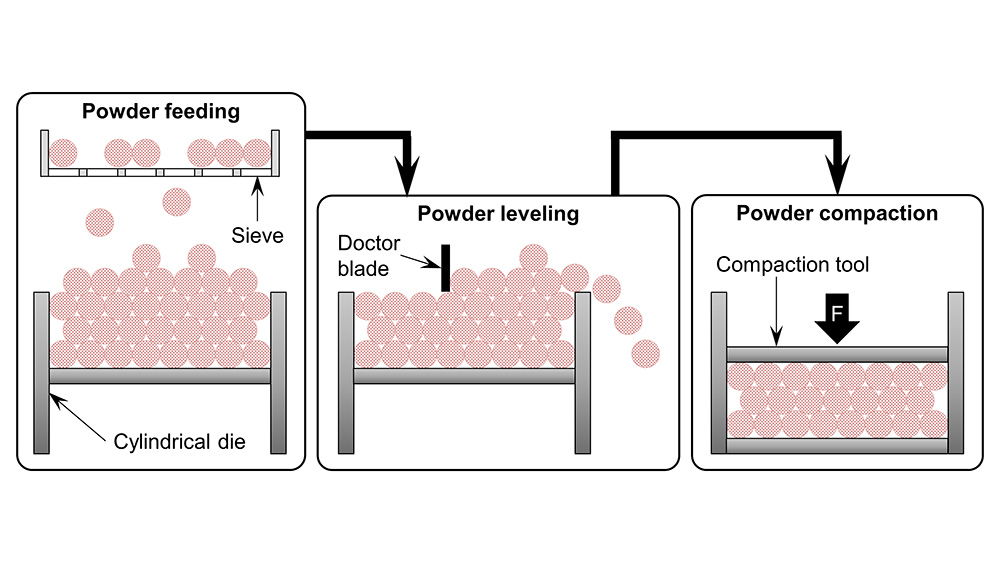
"In terms of research, I hope to increase the properties for ceramic parts from additive manufacturing, and the approach involves powder development and machine-design innovations," he said. "Ceramics are interesting materials. They have excellent properties and are resistant to heat and chemicals. Additive manufacturing can give us freedom in terms of geometry."
To date, no powder allows binder jetting to produce dense ceramic parts. The novel granulated powder consists of smartly tailored granules for density, structure and strength. Ma and his research team will use these granules in an innovative powder bed compaction system to reach the desired density.
They will carry out single and multilayer compaction tests to study the compaction behavior and trace the movement of granules and nanoparticles under pressure through particle-scale numerical simulation.
"It's exciting to me because ceramic additive manufacturing is much less developed, and if this technology can enhance it, then it will bring a lot of benefits to society," Ma said.
As part of the CAREER award, Ma will also focus on education and outreach of this new technology to various audiences, including primary educators and students, undergraduate and graduate students, researchers and the general public to strengthen and diversify the advanced manufacturing workforce.
Education is a big part of this project, and I would say equally important to the research. This creates a big impact and inspires the younger generations.
Ma will host several primary educators in the lab to help them develop teaching materials for their students. Undergraduate and graduate students will work directly on the research and collaborate with industry partners, and Ma plans to create a YouTube channel on ceramic additive manufacturing.
Ma received his bachelor's degree from Tsinghua University in 2010, his master's degree from the University of Wisconsin–Madison in 2012, and his doctoral degree from the University of California, Los Angeles in 2015, all in mechanical engineering. He was a senior mechanical engineer at Cymer from 2015-16 before joining Texas A&M.