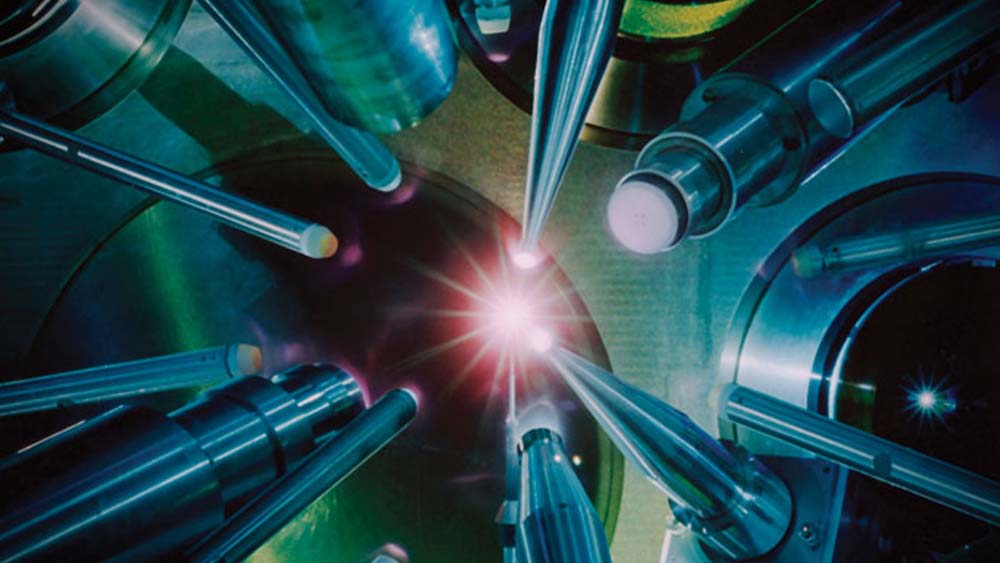
In August 2021, scientists at the Lawrence Livermore National Laboratory’s (LLNL) National Ignition Facility (NIF) had a breakthrough. They succeeded in a nuclear fusion energy experiment by using a laser shot to spark an explosion of energy from a peppercorn-sized fuel capsule. Researchers in the Wm Michael Barnes ’64 Department of Industrial and Systems Engineering at Texas A&M University were, and continue to be, part of these efforts to efficiently access fusion energy.
Fusion energy is a natural process in stars like the sun, where two nuclei combine to form a new nucleus. Scientists would like to use this process on Earth as an energy source based on controlled fusion reactions creating a high energy density plasma, a gas so hot that electrons are freed from the nuclei. When these electrons and ions fuse, they release energy.
One method to create this controlled environment is inertial confinement fusion, containing plasma at the correct temperature and density long enough to induce nuclear fusion reactions. LLNL’s technology uses a spherical shell to improve the energy output. A recent experimental study demonstrated the ability to generate more than 1.3 million joules of energy, a marked improvement over previously reported numbers from similar experiments.
Dr. Suhas Bhandarkar, group leader of NIF, said achieving these results depends on the quality of the surface of the shell, among other factors. The shells are polished over a dozen or more steps to create high-quality surfaces. Each step takes about 24 hours to make the surface progressively smoother and more uniform.
Long polishing cycles, however, expose the shells to various risks. Endpointing the polishing process so it stops at the right time can de-risk the process significantly. That is where collaboration with Texas A&M comes in. Dr. Satish Bukkapatnam, professor, and Dr. Yu Ding, Mike and Sugar Barnes Professor in the industrial and systems engineering department, were brought into the project in spring 2019 when a member from NIF visited their labs.
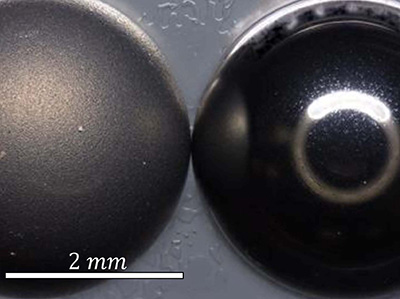
Bukkapatnam said Texas A&M researchers bring experience in smart manufacturing and data science to enhance quality assurance of the components and products critical for the LLNL-led efforts to develop next-generation nuclear fusion reactors.
They had recently investigated using “heightmap” measurements of the surface at the end of each stage of the polishing process to suggest a suitable endpoint.
“One of the challenges in deciding the proper endpoints for such long-stretch, ultraprecision polishing is to account for statistical variation and quantify uncertainty in decisions,” Ding said.
To address that challenge, researchers developed a hypothesis-testing procedure for detecting changes in the surface quality that are more significant than usual fluctuations under polishing. They used data to track representation and detection, which can inform the polishers when to change actions or stop, even in the presence of noises and disturbances.
“The Texas A&M approach and experience in analyzing manufacturing processes has opened up interesting new avenues for resolving our polishing problems,” Bhandarkar said. “Polishing is a critical step for achieving the high quality required for ignition and high energy output.”
The analysis is already providing constructive feedback, revealing that present polishing decisions are possibly conservative and can lead to over-polishing.
“Endpointing a polishing process, in turn, can significantly reduce overpolishing and make the process less vulnerable to defects,” Bukkapatnam said. “Defect-free shells appear to contribute significantly to the performance of a nuclear fusion reaction process.”
Other contributors to the research include industrial and systems doctoral students Shilan Jin and Akash Tiwari and a team of scientists at LLNL. Their latest work was recently published in the journal IISE Transactions.