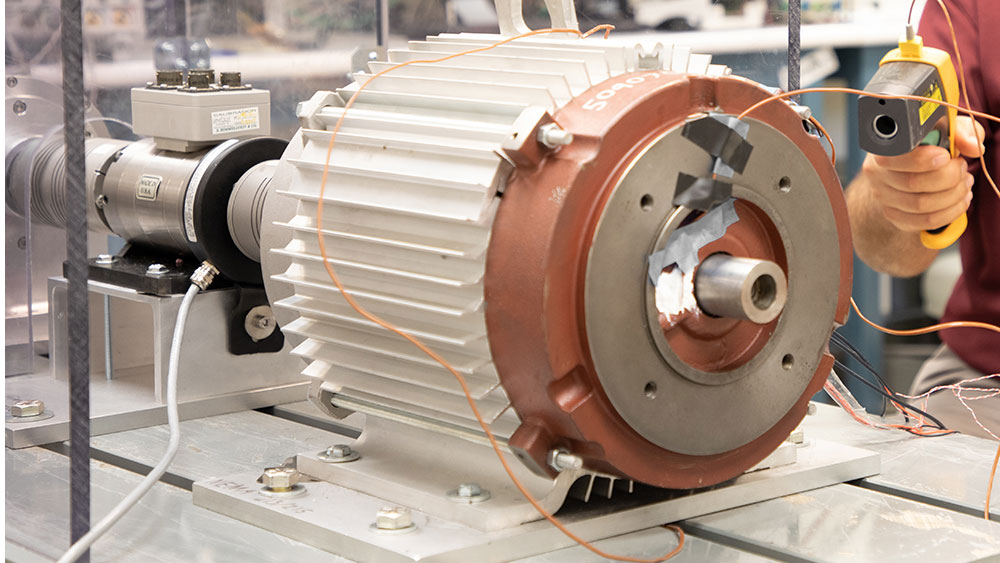
In 2020, the U.S. Department of Energy’s Advanced Research Projects Agency-Energy (ARPA-E) awarded Texas A&M Engineering researchers $1.3 million in funding as part of the Aviation-class Synergistically Cooled Electric-motors with integrated Drives (ASCEND) program. The ASCEND program funding aims to support researchers in developing an all-electric powertrain that will help enable net-zero carbon emissions in single-aisle, 150-200 passenger commercial aircraft.
Electrical engineering doctoral students Dorsa Talebi, Mehdi Seyedi and Erick Pool are working closely with their faculty advisors on different aspects of the project while also collaborating with other graduate students across the college to complete phase one of the project.
Dorsa and Mehdi are working alongside Dr. Hamid Toliyat — their faculty advisor and principal investigator on the project — to configure the design of the electric motor component of the project. To accomplish this, after an extensive literature review to obtain the unique design idea of the most efficient power dense electric motor design, they performed an analysis to evaluate the configuration and dimension of the system utilizing the Ansys Maxwell software, which provides 2D and 3D low-frequency electric field simulation for analysis of electromagnetic and electromechanical devices. Through this process, Talebi was able to design the electromagnetic model motor for the aircraft targeted by the ARPA-E program.
The opportunity to work on a multidisciplinary project like this is very exciting.
Talebi explained that the output of the electromagnetic design of this axial flux dual rotor permanent magnet motor is over 94% efficient, with a peak output power of 250 kilowatts for aircraft takeoff at 5,000 revolutions per minute.
Pool is working alongside his faculty advisor, Dr. Prasad Enjeti on the power electronics component of the project. More specifically, they are working on the design of a multilevel inverter employing Silicon Carbide and Gallium Nitride semiconductors. By employing these semiconductor technologies, they have achieved a lightweight and highly efficient circuit to convert direct current (DC), such as electricity, into alternating current to drive the electrical machine of the aircraft. Pool said the proposed converter is able to deliver a peak efficiency of 99% at peak power (250 kilowatts) and a total mass, excluding the cooling system, of 1.5 kilograms has been achieved.
The Texas A&M team is led by Toliyat. It includes many collaborators across the College of Engineering, including faculty and students from the Department of Electrical and Computer Engineering, the Department of Aerospace Engineering, the Department of Materials Science and Engineering and the J. Mike Walker ’66 Department of Mechanical Engineering.
Talebi and Pool agree that though the process has had its challenges, the multidisciplinary aspect of this project is the key to achieving the milestones they have up to this point.
“The opportunity to work on a multidisciplinary project like this is very exciting,” Talebi said. “This is how industry actually manufactures products. I believe that in the market there is no single electrical group working on the entire project — multiple teams with different expertise are working together. The knowledge I’ve gained from other teams on this project has been crucial for my design.
As they are closing phase one of the project, they are fabricating a portion of their powertrain design to validate their modeling and simulation analysis.