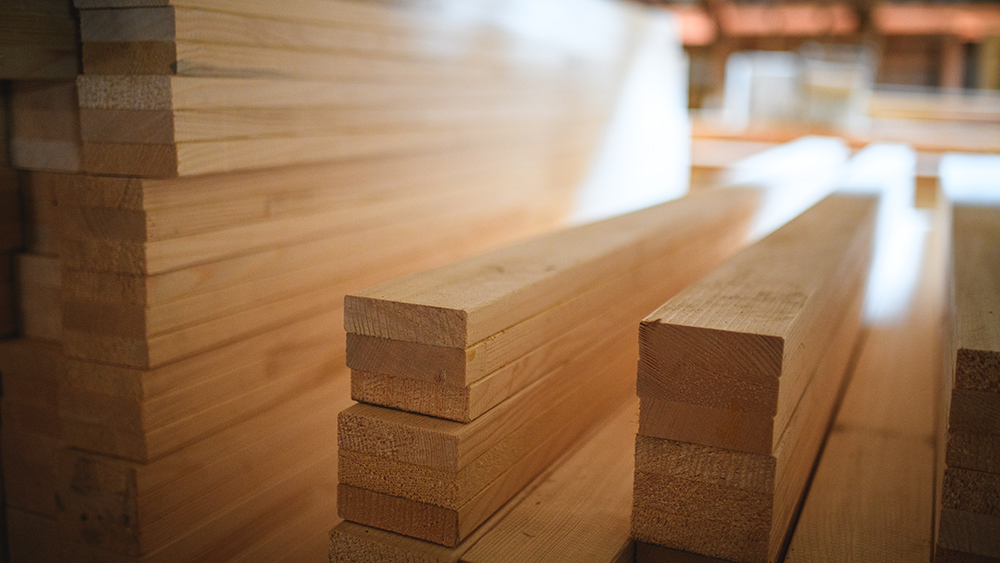
Drying is an essential part of the product manufacturing industry, which accounts for up to 25% of the national energy consumption of developed countries. With the support of the U.S. Department of Energy, researchers from the J. Mike Walker '66 Department of Mechanical Engineering at Texas A&M University are employing their expertise to significantly reduce energy consumption in a specific area — the wood-drying industry.
The project is jointly led by Dr. Zheng O'Neill and Dr. Bryan Rasmussen as part of a multi-million-dollar initiative to reduce industrial emissions and manufacture clean energy technologies. O'Neill serves as associate professor and J. Mike Walker '66 Career Development Professor, and Rasmussen serves as Leland T. Jordan Professor II. The team is also supported by the Texas A&M Engineering Experiment Station through the Energy Systems Laboratory’s Industry Assessment Center.
Nearly 15,000 companies in the U.S. make up the wood product manufacturing industry, and the energy-intensive kiln drying process greatly contributes to the large energy consumption of the industry. The team's proposed shift in wood-drying — mainly known as kiln drying — technology could provide improved energy efficiency, more unified product quality and increased throughput, and reduced reliance on fossil fuel sources.
"With the proposed desiccant-assisted heat pump system, we aim to achieve at least 25-30% energy consumption reduction, 40-50% carbon intensity reduction and 25% operation cost reduction," said O'Neill. "If successful, this project will help the wood-drying industry achieve carbon pollution-free electricity by 2035."
The technology and methods the team seeks to use in this project include dehumidification, low-cost Internet of Things sensors, data assimilation and model-free predictive controls to intelligently and safely operate the drying process.
The project will apply a three-module drying system which is set to be the first example of a kirigami-based heat exchanger system alongside innovations in desiccant-assisted heat pumps. The third component of the three-module system will be an intelligent deep-reinforcement learning-based product-centric controller.
Although this project is primarily focused on wood drying, O'Neill noted that the principles of the system could also be applied to various other drying applications, like food or textiles. In addition, the proposed heat pump innovations will have wide applications for heating, ventilation and air-conditioning in buildings to promote building decarbonization through electrifications.
An additional objective of the research is to involve students from underrepresented minority groups in STEM by collaborating with minority-serving institutions and offering training and workshops on the technologies and industry drying process in underserved communities and economically disadvantaged areas.
In addition to O'Neill and Rasmussen, partners on the project include Dr. Shu Yang from the University of Pennsylvania, Dr. Cindy Chang from the University of Virginia, Dr. Xinfeng Xie from Michigan Technological University and Dr. Andy Pascall from Lawrence Livermore National Laboratory.