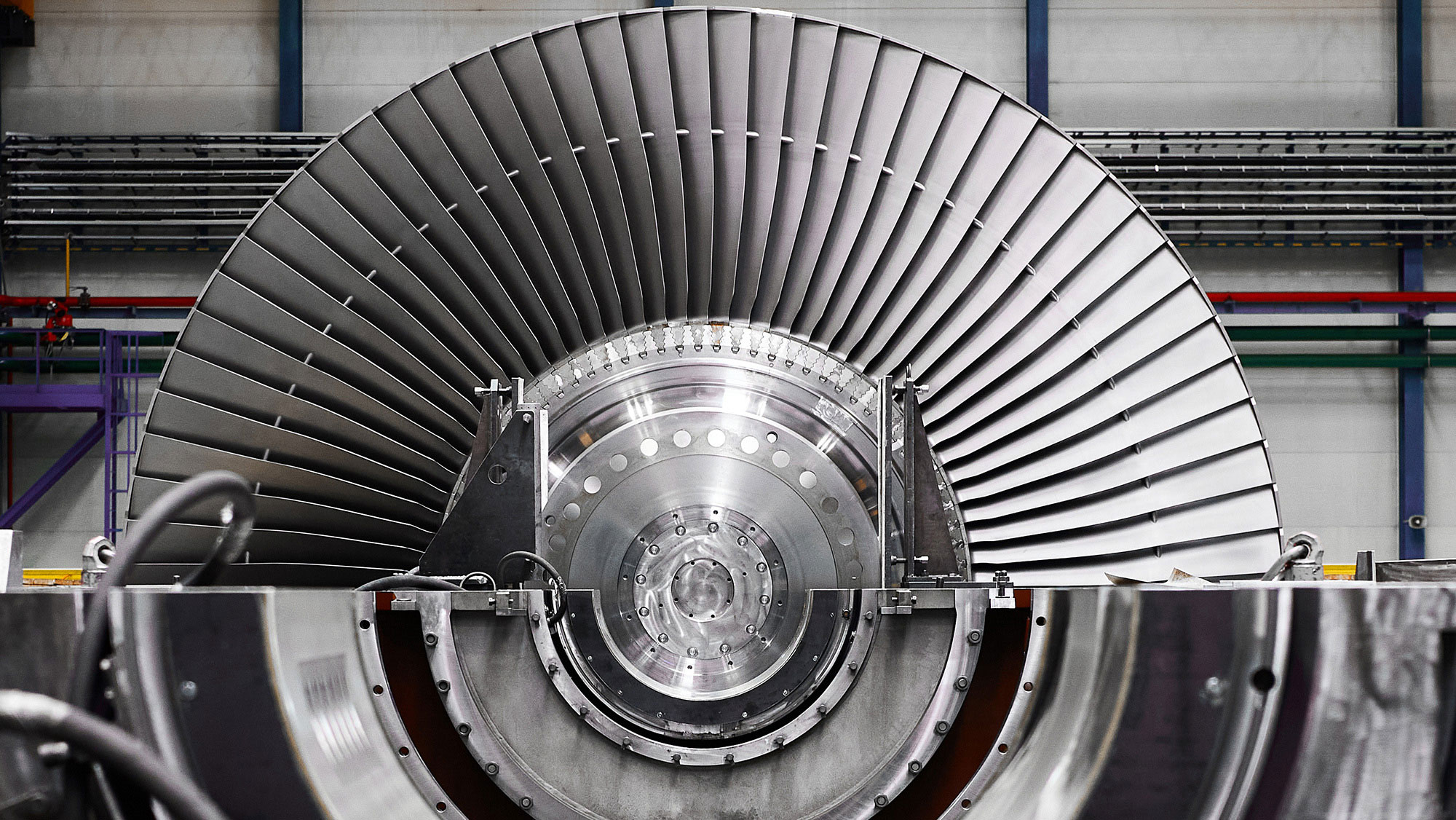
In 1884, marine engineer Charles Parson used coal to power his groundbreaking invention, the multi-stage steam turbine, to produce electricity. This technological revolution marked a new dawn of power generation and consumption around the world. Today, humanity’s increasing electricity and power needs require more efficient turbines and environmentally friendly fuels.
To meet the energy needs of the near future through breakthrough materials technology, engineers at Texas A&M have been granted funding by the Department of Energy. With this support, their goal is to develop a materials system for gas turbines that can operate using hydrogen fuel instead of natural gas. This will include high-performance alloys, protective coatings and cooling systems.
“The United States has set an ambitious goal to decarbonize energy by 2035,” said Dr. Don Lipkin, professor in the materials science and engineering department and principal investigator on the grant. “We need materials solutions for advanced gas turbines that are both cleaner and more efficient; that is, the turbines can work at much hotter temperatures and use hydrogen gas instead of natural gas so as not to produce carbon dioxide.”
Turbines convert mechanical energy to electrical energy. Within these machines, blades attach to a central shaft. When these blades rotate, like the blades of a fan, the shaft spins, turning a generator and producing electricity. In Parson’s turbine, the blades were set in motion by the steam produced by coal-heated water. In the 1930s, coal-fired power plants slowly started to shift to natural gas to improve power production efficiency and reduce carbon dioxide emissions. In gas turbines, the pressure from ignited compressed gas turns the blades to produce electricity instead of steam.
The goals for the next generation of advanced turbines are to be even more efficient and replace natural gas with hydrogen, which has a minimal carbon footprint. However, these goals open two other cans of worms.
The United States has set an ambitious goal to decarbonize energy by 2035. We need materials solutions for advanced gas turbines that are both cleaner and more efficient; that is, the turbines can work at much hotter temperatures and use hydrogen gas instead of natural gas so as not to produce carbon dioxide.
“Very efficient turbines need to operate at much higher temperatures, around 3000 Fahrenheit or more, and we need materials solutions for advanced turbines that can operate in these hotter regimes,” said Lipkin. “The other problem is that when you burn hydrogen in air, you make more steam than when burning natural gas. Most turbine materials will show signs of accelerated distress when exposed to high temperatures and very wet environments.”
The materials used to make turbines are superalloys that are composed of predominantly nickel and cobalt, with small quantities of other elements, such as chromium, aluminum, tungsten, molybdenum and niobium. The main problem with nickel-based superalloys is that they begin to melt at 2400 F. Hence, engineers are investigating a new class of materials system called refractory high entropy alloys (RHEAs), many of which have melting temperatures above 3500 F. Under Phase 1 of the Advanced Research Projects Agency-Energy (ARPA)-E’s ULTIMATE program, Texas A&M materials scientist Dr. Raymundo Arróyave identified promising a number of promising RHEAs.
“To solve this seemingly impossible problem, we make use of advanced alloy design tools pioneered in our groups,” said Arróyave who is co-principal investigator in this project along with Dr. Ibrahim Karaman. “The discovery of new alloys capable of withstanding these extreme environments is akin to finding a needle in a multi-dimensional haystack.”
In the next step, Lipkin and his team will test if RHEAs with tailored coatings developed by the A&M team can simultaneously tolerate high temperatures, oxidation and moisture. They are creating an experimental set-up closely resembling the hottest portion of a hydrogen-fired gas turbine. Simply put, highly pressurized hydrogen and air will be squeezed through small rocket-nozzle shaped tubes and ignited. This process generates hot, high-velocity gas and steam that exit the nozzle at supersonic speeds and impinge on the RHEA coupons.
The team will investigate the resilience of the RHEA materials system — including the substrate alloy, oxidation-resistant coating and thermal barrier coating — in a simulated hydrogen gas turbine environment with and without cooling.
“One way we can meet our carbon reduction goals in the energy sector is to keep our overall energy generation infrastructure intact but switch to burning hydrogen as the fuel, as opposed to natural gas,” said Lipkin. “No one solution is going to work for all of the energy infrastructure in the US; it’s going to be a mix of renewables and non-renewables.”
Funding for this research is administered by the Texas A&M Engineering Experiment Station (TEES), the official research agency for Texas A&M Engineering.