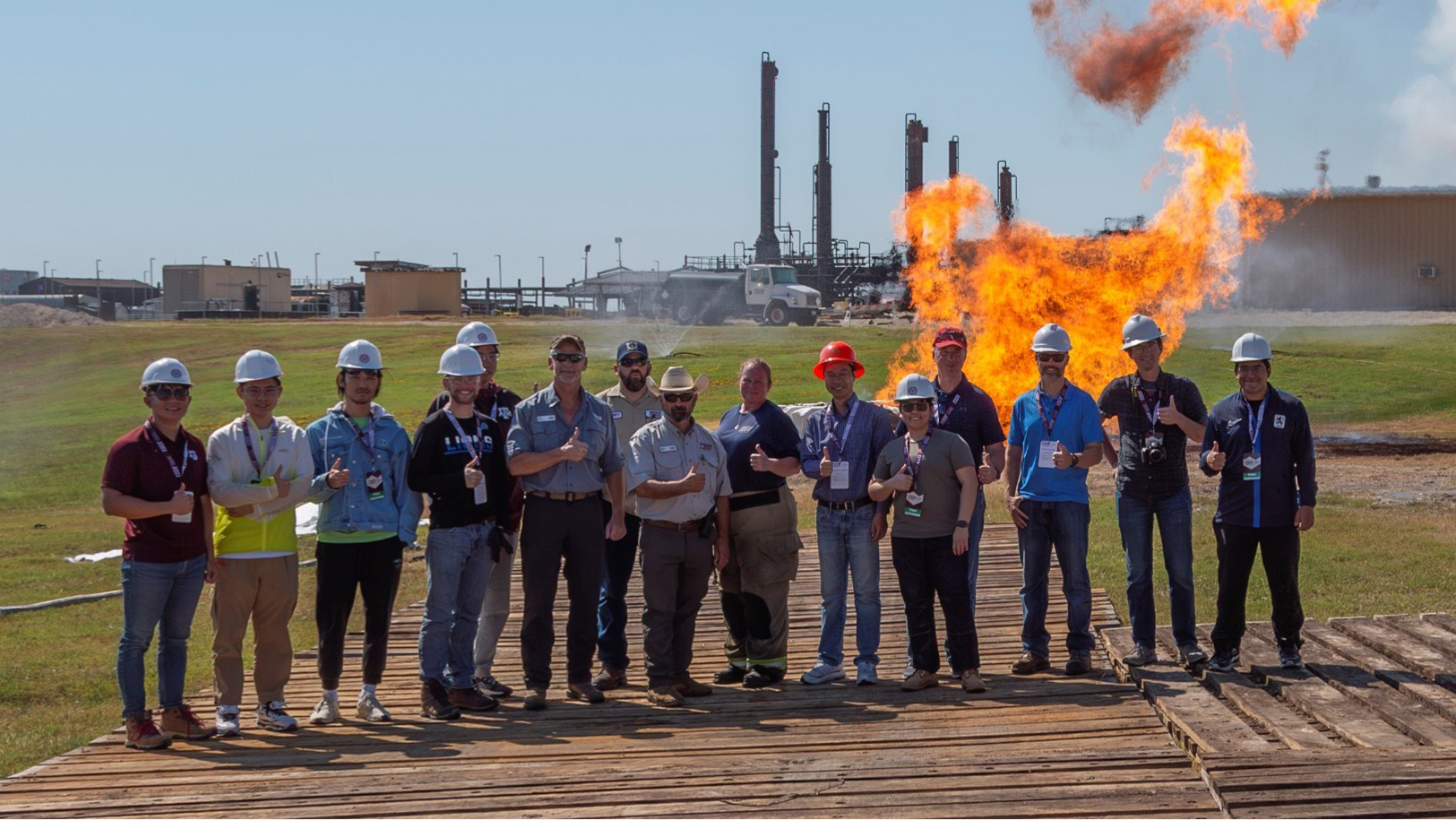
Enhanced safety measures are being made for structures that are exposed to liquefied natural gas (LNG) fire.
Dr. Filippo Gavelli from Blue Engineering and Consulting Company (BLUE) and Dr. Qingsheng Wang, a professor with the Department of Chemical Engineering, have led a large-scale experiment testing different coatings on steel beams and examining how they hold up in a fire.
The project is a collaboration between BLUE, the Texas A&M Engineering Experiment Station (TEES), and Texas A&M Engineering Extension Service (TEEX). It’s sponsored by the U.S. Department of Transportation (DOT).
Currently, structural steel fireproofing is tested while coated on all four sides; however, in many practical applications, structural beams are only coated on three sides while the top side is left exposed to allow piping support placement.
Part of this experiment is to determine if only coating three sides of the steel beams that make up the structures would sustain the facility in the event of an LNG pool fire.
The project team tested three different mitigation systems that they coated on the beams: cement, epoxy, and foam on both three sides and four sides.
“Through this testing, we collected the data, developed the model, and based on that, we will propose failure criteria for structural steel,” Wang said. “What we want to test is the passive mitigation system and if it effectively delays the temperature increase of the beams.”
To perform this experiment, the project team used a 10 ft by 10 ft pit filled with LNG and stacked four beams over the pit. One bare beam with no coating and the other three were coated with cement, epoxy, or foam.
All experiments were conducted at the TEEX Brayton Fire Training Field. For this project BLUE handled beam preparation and delivery, TEES focused on instrumentation and data collection, and TEEX managed operations and safety.
“The purpose of the project is to obtain data on the thermal response of structural steel exposed to direct flame impingement, to validate models and to provide a comparison with standard test configurations,” Gavelli said. “Additionally, the project wanted to compare the thermal response of steel beams coated on all 4 sides, as typically tested, versus beams with the top flange left uncoated, as typically installed.”
The project team has been in the process of preparing experiments and testing various beams and coatings since early this year.
In the next few weeks, the project team will review the temperature profiles of each beam and analyze the data from calorimeter cubes. The project team will submit a report on the testing results to the DOT in December; however, a final report on the project will not be publicly available until October 2025.
“The potential impact after we send the final report to the DOT could lead to significant changes in the industry,” Wang said. “We are providing scientific evidence, based on the data we collect and the models we develop, to support future regulations.”
Funding for this research is administered by the Texas A&M Engineering Experiment Station (TEES), the official research agency for Texas A&M Engineering.